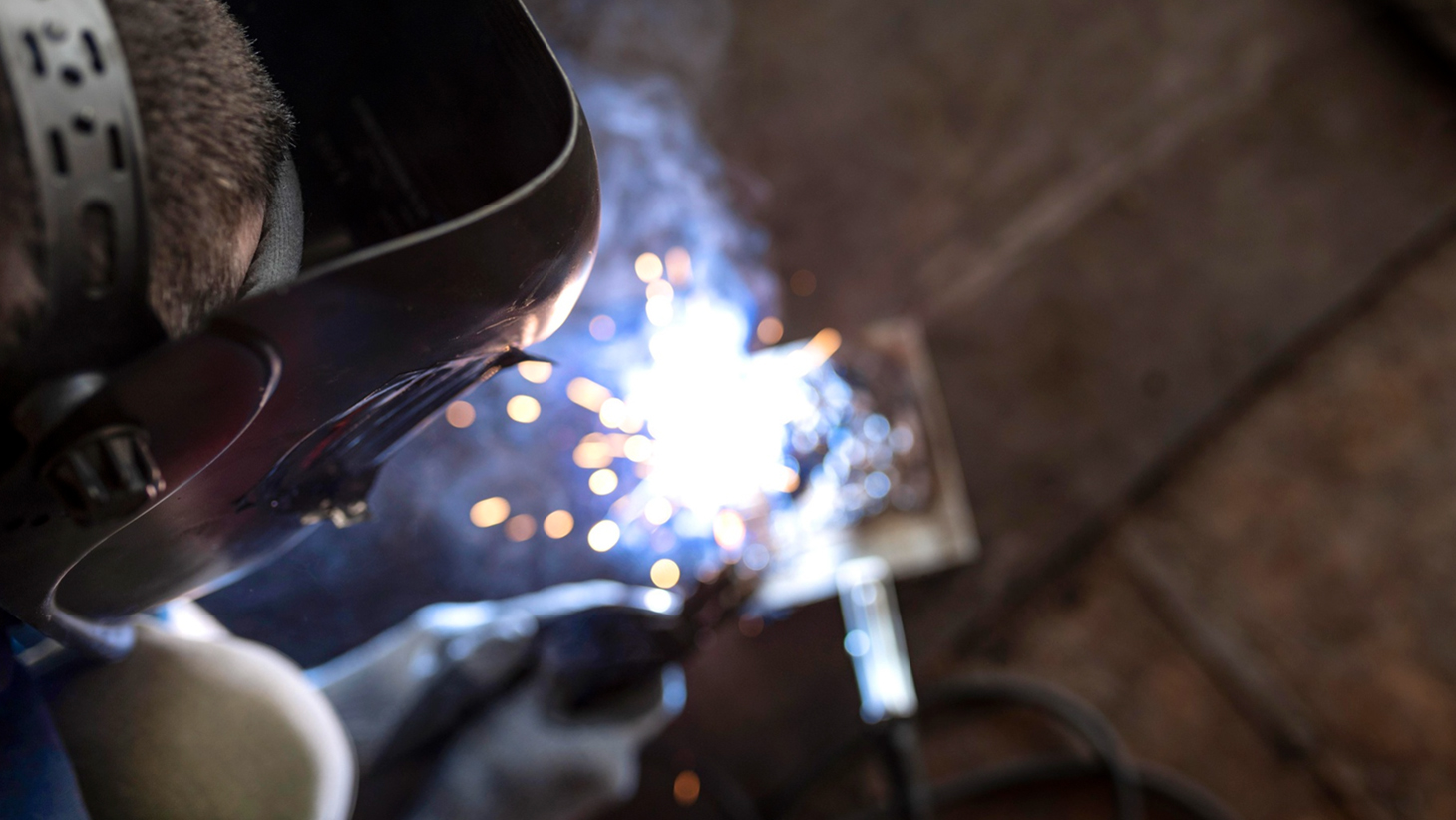
Procesos de soldadura y sus efectos estructurales
La soldadura es uno de los procesos de fabricación más difundidos en diversas aplicaciones industriales, siendo utilizado principalmente para realizar la unión de dos o más componentes. Presenta gran versatilidad debido a las diferentes modalidades existentes, caracterizadas en general por cómo se forma la junta soldada, destacándose los procesos por fusión.
En relación a los ciclos térmicos de calentamiento y enfriamiento involucrados en el proceso, problemas como cambios geométricos y tensiones residuales pueden comprometer el comportamiento estructural de la pieza soldada, motivando así el desarrollo de metodologías para cuantificar y minimizar estos efectos.
Aunque las soldaduras presenten gran complejidad desde el punto de vista físico ya que involucran simultáneamente diferentes disciplinas acopladas entre sí (como transferencia de calor, electromagnetismo y metalurgia), se puede destacar que en los procesos de soldadura por fusión haya una influencia más significativa de los fenómenos término-mecánicos.
El comportamiento térmico es el responsable del proceso de fusión entre los diferentes componentes, el cual es estimulado a partir de la presencia de una fuente de calor. Este proceso puede ocurrir varias veces en las soldaduras con más de una etapa, lo que genera un ciclo térmico con consecuencias estructurales en los componentes.
Los principales efectos estructurales son distorsiones geométricas y tensiones residuales. En forma general, el nivel de restricción al movimiento de la junta es el responsable por la magnitud de cada uno de esos fenómenos. Componentes que tengan poca o ninguna restricción (mayor libertad el movimiento) tienden a estar más sujetos a distorsiones; por su parte, aquellos que presenten mayores restricciones serán sometidos a campos de tensiones residuales más significativos.
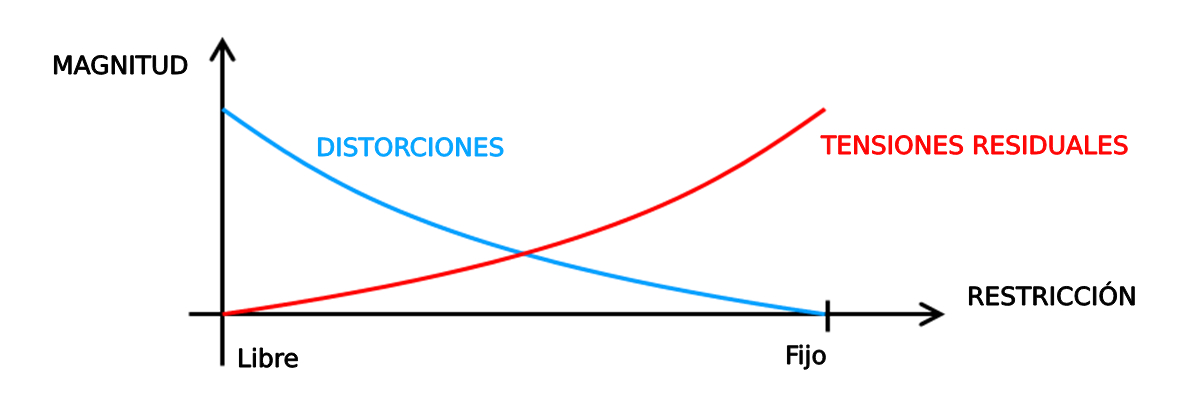
Curvas características de los fenómenos que actúan sobre una junta soldada en base a su grado de libertad
Las distorsiones geométricas corresponden las variaciones de forma y/o dimensiones del componente soldado después del enfriamiento y están asociadas a las deformaciones plásticas permanentes provenientes del proceso. Además de esto, el retorno elástico ocurrido luego de la liberación de las sujeciones aplicadas durante la soldadura, también contribuye al surgimiento de distorsiones.
Las deformaciones geométricas pueden ser significativas al punto de comprometer la operación o el montaje del componente soldado. Por otra parte, dichas distorsiones pueden ser clasificadas según su configuración final, tal como contracción longitudinal y/o transversal, angular o flexión, entre otras.
Las tensiones residuales representan un estado de solicitud mecánica a la cual estará sometido el componente inicialmente para luego ser sumadas las tensiones de operación, pudiendo resultar en esfuerzos críticos por encima de los límites aceptables de proyecto. Dichos esfuerzos iniciales también tienen influencia en la respuesta a la fatiga del material, la cual puede ser benéfica o prejudicial en función del comportamiento del componente a compresión o tracción, respectivamente.
En las uniones soldadas, las tensiones residuales son causadas principalmente por el campo de temperaturas no uniformes y transitorias durante el proceso, así como por fenómenos de transformaciones microestructurales del metal.
Con el fin de minimizar la magnitud de estas tensiones residuales, diferentes técnicas pueden ser empleadas durante el proceso de soldadura tales como la optimización geométrica del bisel de soldadura, el control de la tasa de deposición del material de aporte o el pre-calentamiento de la junta.
En el caso de que sea viable, también es posible aplicar tratamientos térmicos para el alivio tensional. A diferencia de las distorsiones, las cuales son evaluadas directamente en la geometría, el relevantamiento experimental de las tensiones residuales muchas veces sólo es posible por medio de ensayos destructivos y no son aplicables para el estudio de componentes en servicio.
Modelado Numérico Aplicado a Soldaduras
Debido a la criticidad de los fenómenos estructurales mencionados, la soldadura ha sido foco de diversos estudios e investigaciones científicas en los últimos años. El principal objetivo es buscar soluciones basadas, no sólo en ensayos experimentales, sino también en modelado numérico, permitiendo prever el comportamiento estructural de las uniones soldadas.
Un ejemplo consiste en la aplicación del Método de los elementos finitos para el modelado término-estructural del proceso de soldadura, mediante la representación numérica idealizada de una fuente de calor y el empleo de propiedades del material dependientes de la temperatura para estimar los ciclos térmicos y de esta forma poder caracterizar el perfil de tensiones residuales después del proceso.
Cabe resaltar que actualmente ese tipo de evaluación numérica posee algunas restricciones y limitaciones que pueden restringir su aplicación. Muchos parámetros e informaciones fundamentales para este tipo de análisis aún dependen de datos obtenidos experimentalmente, en especial para la correcta representación de la fuente de calor de la soldadura.
Además de esto, algunas geometrías de cordones de soldadura son relativamente complejas, lo cual exige cierto nivel de simplificación numérica para viabilizar el estudio. Esto es más significativo en soldaduras con múltiples etapas, lo que requiere un mayor esfuerzo computacional.
Aunque el modelado numérico de soldaduras actualmente es un tema con más presencia en los medios académicos, puede proporcionar a los ingenieros un mayor conocimiento de las consecuencias de este proceso en el comportamiento de los elementos y estructuras soldadas, permitiendo prever o evitar eventuales fallos, como así también mejorar el proyecto, teniendo en cuenta la influencia de las uniones soldadas.
También es importante destacar que el constante aumento de la performance computacional contribuye para hacer más factible este tipo de estudios, de modo que es cuestión de tiempo que el modelado numérico en procesos de soldadura sea aplicado en problemas reales de ingeniería, ayudando a los profesionales.