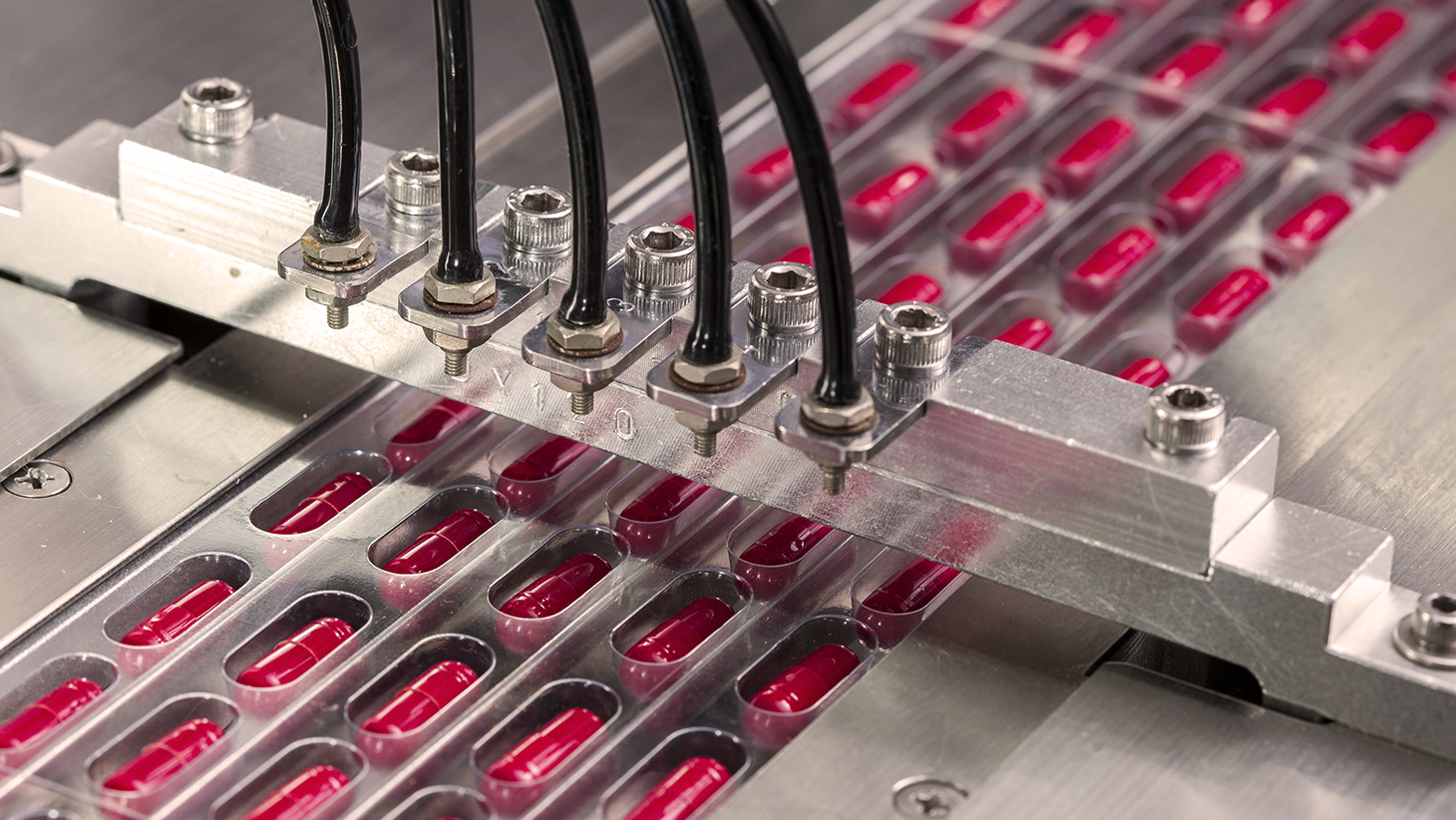
Cómo los experimentos in silico están revolucionando la industria farmacéutica y de dispositivos médicos
La simulación computacional es una realidad presente en la gran mayoría de las industrias que se ven impulsadas por la innovación para crear mejores procesos y productos. La industria farmacéutica está apostando por experimentos con simulación computacional –in silico– para el desarrollo de nuevos fármacos y dispositivos médicos, permitiendo seleccionar los resultados más prometedores y lograr optimizar la fase de pruebas in vitro.
El modelado y la simulación computacional ayudan a acelerar los procesos de desarrollo, a crear productos más eficaces y seguros y a reducir costos. En Estados Unidos, por ejemplo, lanzar un nuevo medicamento al mercado puede llegar a costar cerca de 2 mil millones de dólares.
Cuando la simulación se lleva a cabo al inicio del proceso, es posible prever fallas y seleccionar los dispositivos o fármacos con mejor rendimiento en su fase inicial, para luego llevar a cabo las pruebas in vitro, reduciendo el tiempo de banco necesario para desarrollar un nuevo producto.
En el caso de no haber llevado a cabo la simulación al inicio y que el producto no funcione, es posible utilizar las pruebas in silico para descubrir el motivo de dichas fallas y desarrollar soluciones para los problemas detectados.
En ambos casos, es muy importante que el equipo técnico especializado en el área de la salud cuente con la ayuda de profesionales con experiencia en simulación.
Estudio de caso: confiabilidad electrónica en dispositivos médicos
Una importante empresa de dispositivos médicos, se encontraba con dificultades para descubrir la causa de fallas en uno de sus dispositivos electrónicos, ya que las pruebas del producto no mostraban los mismos tipos de fallas que el componente presentaba en servicio. Dicha empresa requirió del equipo de Ansys Reliability Engineering Services (RES) para ayudar a descubrir las posibles causas y resolver los problemas.
Los especialistas en confiabilidad electrónica de Ansys trabajaron directamente con el fabricante del dispositivo. El objetivo era comprender las fallas observadas, el diseño del dispositivo y el entorno donde se utilizaba antes de seleccionar los casos de uso de la simulación, para no tener que simular todos los casos de uso posibles, evitando así un proceso más costoso y lento.
Combinando décadas de experiencia en confiabilidad electrónica con herramientas de simulación y modelado, fue posible evaluar los riesgos de falla bajo carga operacional térmica, de choque y de vibración, lo que resultó fundamental para una rápida identificación del mecanismo de falla.
Esta geometría de modelo simplificada y el enfoque de malla optimizada se centra en las características de diseño críticas que pueden afectar la confiabilidad bajo las cargas operativas específicas del dispositivo – minimizando la configuración de la simulación, los tiempos de ejecución y el tiempo del ciclo de proyecto.
El análisis resultante identificó componentes que excedían los límites de proyecto en condiciones normales de funcionamiento, lo que provocaba fallas de desconexión del dispositivo observados en servicio. Además de identificar el mecanismo de falla, el trabajo demostró el valor de la simulación y modelado robusto como una parte integral del proceso de diseño para identificar y mitigar las fallas potenciales antes de que aparezcan en el producto final.
Con estos resultados, los ingenieros de proyecto del fabricante, lograron eliminar áreas de proyecto excesivo (reduciendo costos), reforzar áreas seleccionadas del proyecto para mitigar el riesgo de fallas y optimizar la elección de materiales, las tolerancias y la estrategia de ensamblaje.