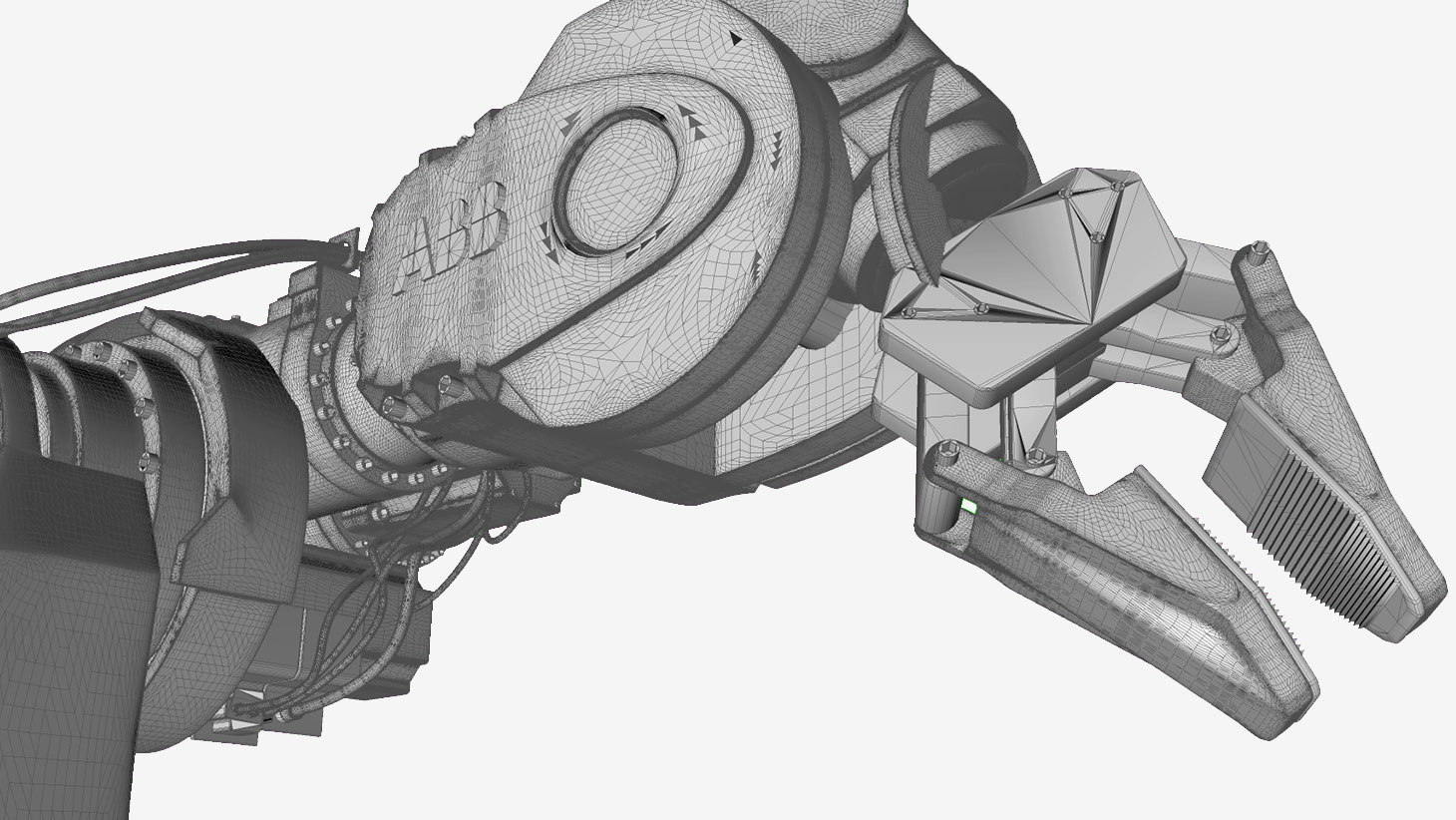
Cómo crear un digital twin
Actualizado el 18 de junio de 2021
La Internet Industrial de las Cosas (IoT) se revela a medida que las empresas utilizan tecnologías nuevas y en rápida evolución. El concepto más reciente es el digital twin, que combina datos digitales y operativos de recursos industriales con una plataforma de software, simulación y análisis para obtener información sobre operaciones presentes y futuras. El resultado es una mejora en la producción, costos reducidos, innovación acelerada y, finalmente, una solución que es mucho más que un producto: es el resultado que la industria exige.
La IoT saltó desde las aplicaciones del consumidor, que facilitan la simple interacción y colaboración, y líderes de la industria, como General Electric (GE), amplían esa conectividad para operar las máquinas. El resultante Internet industrial de las cosas (IIoT) permite a las organizaciones comerciales involucrarse con grandes máquinas complejas (por ejemplo, turbinas eólicas y de gas, motores a reacción, locomotoras) para mejorar el rendimiento, reducir el tiempo de inactividad y acelerar el desarrollo de nuevos productos. Y ello no se detiene ahí. Los modelos de coste de hoy para la tecnología de sensores, la conectividad a Internet, y simulación y análisis permiten la conectividad no sólo con máquinas altamente complejas e intensivas en capital, sino con casi todos los equipos en operación.
Datos e Internet Industrial
El IIoT, en práctica, se utiliza más para determinar o sugerir una acción: por ejemplo, instruir a una turbina eólica para que incline sus rotores para mejorar la exposición al viento. En primer lugar, los datos del sensor recopilados de los recursos se agregan a cualquier otra información digital disponible. Un panel combina esa información con los datos de tiempo real y de rendimiento esperado del equipo para producir análisis descriptivos, que logran predecir posibles fallos y el mantenimiento del cronograma. El paso final es la optimización, que toma en cuenta los recursos individuales en todas sus configuraciones junto con los sistemas de recursos para llegar a múltiples soluciones. El objetivo es optimizar un ecosistema muy complejo en torno a un recurso específico. Los modelos muy ricos que describen la estructura, el contexto y el comportamiento de los recursos industriales se llaman digital twins.
Este rendimiento mejorado tiene un costo: el IIoT administra enormes cantidades de datos, extrayendo información y obteniendo ideas prácticas a través del análisis de big data y aprendizaje profundo. Por seguridad y también para administrar la cantidad de información, algunos datos se almacenan y procesan localmente “en la frontera”. Otras funciones se ejecutan en datos en la nube. Este enfoque híbrido de la punta a la nube ayuda a administrar la cantidad de datos y permite un enfoque computacional mejor para diferentes tipos de objetivos, manteniendo la seguridad y la protección de la operación y protegiendo la valiosa IP de la empresa.
Cómo empezar a utilizar un digital twin
Un gemelo digital o digital twin comienza con un modelo básico que describe el recurso. Por ejemplo, un modelo de turbina eólica puede contener información del sistema PLM con detalles sobre materiales y componentes, un modelo geométrico 3-D, un modelo de simulación que predice el comportamiento esperado con base en algoritmos físicos o recomendaciones de análisis creados usando técnicas de aprendizaje automático. El modelo puede también incluir registros de mantenimiento y detalles de defectos y soluciones, capturando todo el ciclo de vida del recurso.
Inicialmente, el digital twin representa una clase de recursos (en este ejemplo, una turbina eólica del tipo x). Este “gemelo genérico” debe ser individualizado para una turbina eólica específica en un lugar específico. Considere que la máquina funcionó por cinco años, soportando un clima específico para su ubicación, funcionando entre las 50 otras turbinas. Por lo tanto, se debe modelar todo el parque eólico. Cada turbina es semejante, pero lleva diferencias basadas en su posición o experiencia (dirección del viento, registro de mantenimiento, efectos de vigilia). Al final, la rica representación del digital twin contiene su condición pasada y presente momento por momento. El futuro de una turbina eólica específica, en este caso, está codificado en ese digital twin.
Los digital twins proporcionan imágenes operativas precisas de los recursos en el momento. Hay un valor comercial importante en la identificación de dispositivos subutilizados, así que analizar información doble puede conducir a un uso ideal. Por ejemplo, GE Power utilizó un digital twin para obtener un 5% más de potencia de un parque eólico sin realizar grandes cambios. El equipo optimizó las turbinas para las condiciones cambiantes del viento y organizó la interacción de gemelos individuales en el lugar. Una visión parecía anti-intuitiva: en situaciones específicas, desconectar algunas turbinas mejoró la producción en comparación con la operación de todas las turbinas. Al predecir posibles problemas de una forma individualizada, los operadores pueden programar el mantenimiento para disminuir la interrupción del servicio. Una vez que la información se codifica en un sistema de recursos, el equipo puede tomar ese conocimiento y convertirlo en acciones que alcanzarán los resultados deseados.
Construir un digital twin al principio es la clave para crear un conjunto rico de aplicaciones que produzcan resultados relacionados con recursos, no sólo desarrollar un panel para la toma de decisiones del operador de equipos. Un digital twin con recursos completos facilita el desarrollo y la implementación de aplicaciones posteriormente. La física, la analítica y la información de simulación dentro del modelo abre el camino para el aprendizaje de las máquinas.
Simulación y gemelo digital
Durante décadas, GE reunió datos sobre muchos recursos, como motores a reacción. Combinar estos datos con modelos estadísticos predice lo que es probable que suceda y cuando, pero es insuficiente determinar por qué y cómo sucede. La adición de la simulación basada en la física es el último paso para obtener esta visión extra. Predix, la plataforma digital de GE para la Internet Industrial, puede sobreponer datos con simulación en un contexto industrial, que funciona como un modelo común de datos. Las simulaciones se pueden ejecutar en el sitio o en la nube, empujando los modelos hacia la frontera y devolviendo a la nube la información que estos crean. La integración completa exige la conexión al sistema de PLM del cliente, vinculando los datos de CAD y otra información valiosa registradas en los sistemas corporativos. Un digital twin que se basa en un modelo común e incorpora muchas fuentes de información enriquece el conocimiento.
GE Digital aprovecha la simulación de Ansys en sus digital twins, de modo que ambas organizaciones se beneficien inmediatamente de la colaboración. El mayor valor de los software Ansys está en reunir diferentes aspectos de la simulación, por lo que ayuda a los proyectistas a pensar completamente en sus proyectos. Debido a que un modelo de simulación demuestra cómo funcionan los recursos, el doble enfoque muestra exactamente cuando la operación es incorrecta. Los digital twins toman resultados de simulación y de la vida real para proporcionar información inmediata sobre un producto. En breve, la tecnología permitirá optimizar un recurso individual en el campo, que se podrá implementar durante todo el ciclo de vida de un equipamiento o sistema.
El futuro
Los digital twins se pueden aplicar prácticamente en casi todos los sectores: transporte, energía, aviación y muchos otros. Las empresas ya están ahorrando con la reunión de datos, la simulación, la plataforma, funciones en la nube, y el aprendizaje automático. Y los beneficios futuros son prometedores a medida que el concepto de dos digital twins crece constantemente.