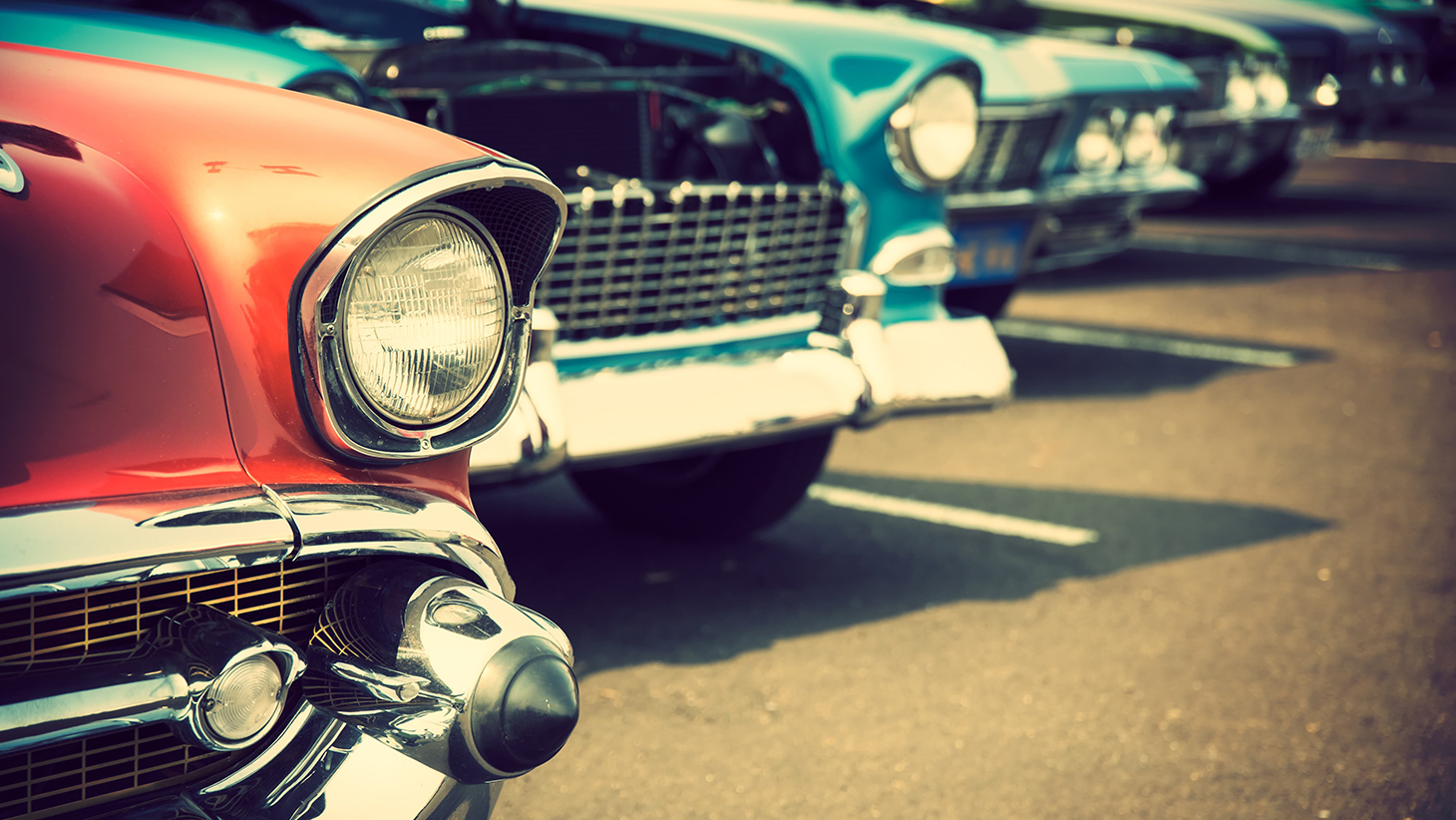
What is reverse engineering?
When we are in college, it is common to wonder what our life will be like after we graduate. What the job will be like, where we will live, what places we will visit. I wanted a car. It took me 3 hours to go to college and 3 hours to come back, so I converted all the savings from my internship into a 1.0 vehicle, year 95. It was a landmark of my car: rusty bodywork, a gallon of water to top up the radiator fluid level along the way, spare fuses and battery cables in case of an unexpected breakdown (and yet part of me feels that it was the best car I ever owned).
As the profession progresses, I begin to have professional growth and trade my car for a modern, more economical, more onboard technology, small and agile, meeting the current demands of the increasingly innovative automotive sector. This phase did not last long: the children came, and everything they carried with them – car seats, bags with food, diapers, strollers, toys. And my small, agile, modern car simply lost its function. So we went back to the research and wonder: big cars, with comfort, designed for large families, have a cost equivalent to their usefulness. Without further ado: I am back to the reality of an old/classic car.
Elegant curves, a powerful and not at all economical engine, unique comfort and sound experience. For enthusiasts in this subject, one of the biggest problems to be faced is the need for a discontinued part. And this is not a reality exclusively for the automotive industry.
The Use of Reverse Engineering in the Industry
Aircraft, industrial machinery, agricultural equipment, household appliances, and others can outlive their design life, making parts hard to find. How do you fix a machine when you can’t find the part you need?
The answer is reverse-engineering – the action of recreating an existing design to replicate or replace parts that are impossible or difficult to obtain in any other way. This way it is possible to repair old equipment or help engineers create designs to support third-party products.
The basic process is to replicate the part digitally – usually in computer-aided design (CAD) software. The digital geometry is created manually or using a scanner to take advantage of the previous part. Once the geometry is recreated, the engineer can then build the part using traditional or additive manufacturing methods.
Replicating lost manufacturing methods using Scan-to-CAD technology
You could say that reverse engineering is like an archaeologist who has discovered a part created by a previously unknown manufacturing process during excavation. With reverse engineering, the archaeologist can recreate parts of that machine, so that it will be completed in a museum exhibit.

Engineers using additive manufacturing to recreate a device
In the engineering world, the reasoning is the same. Especially maintenance engineers know what it is like to repair and retrofit equipment that has been in operation for 60 years or more, and often the very design of the device is old technology, if not non-existent.
How to use reverse engineering using Scan-to-CAD technology
The first step in a reverse engineering workflow is to accurately capture the dimensions of the part you would like to recreate. This can be painstakingly done manually, but for many parts, this is not practical. Fortunately, today’s 3D scanners automate this work and are available in various price ranges. The 3D scanner will measure the part as it forms a point cloud. You can think of this cloud as a series of points on a Cartesian plane. The scanner software will then transfer the point cloud into an STL file.

An engineer scans a piece of equipment so it can be recreated in CAD.
A 3D scanner can be as simple as a telephone camera or as complex as a laser scanner on a robotic arm. The better the scanner, the more detailed the point cloud is. However, inadequate scan data is common in the engineering world. Therefore, it is better to have access to tools that work on this STL file with imperfections.
Ansys Discovery
Ansys Discovery has STL repair tools that can fill in missing patches, holes, and faces, and then combine the result into the remaining geometry. This is useful for recreating asymmetrical parts when you only have half of the original, or filling in the missing teeth of a gear, for example. If the original part is deformed, you can use Discovery to digitally repair it back to its original shape.

Ansys Discovery can be used to transform a scan into a 3D model suitable for fabrication.
The potential use is unique: engineers can finally obtain new parts that are no longer available on the market. Once the geometry has been digitized, it is also possible to verify this past design from a digital prototype and check its reliability, as well as extrapolate the original design and create a new part using the topological optimizer present in Discovery, obtaining new geometries that are lighter, more innovative, and more resistant than the original design. In this way, if the engineer has a 3D printer at his disposal, he can print the result of this process and practically validate the result obtained from the digital prototype.
In other words, I could use this technology to create new parts for my car. As tempting as the idea is, I find it difficult to convince my audience with this argument alone. Who knows, maybe the possibility of creating new toys together with the children and having real father and son moments will be a greater motivator for this desire to become a reality. In the meantime, you can get a free trial of Discovery to test it out.