
Conheça as duas ferramentas mais eficazes para reduzir custos com garantia
No mundo da alta tecnologia, confiamos em eletrônicos para nossa saúde, segurança, mobilidade e bem-estar econômico. Quando eles falham, os resultados vão desde pequenos aborrecimentos para o consumidor até consequências tão graves quanto a perda de vidas.
Por esses motivos, é necessário que todos os fabricantes de eletrônicos forneçam uma garantia do produto. Uma garantia, na sua forma mais simples, significa que o fabricante atesta que o produto vai funcionar conforme o esperado, sem falhas, por um determinado período de tempo, em um ambiente especificado.
Na indústria de eletrônicos de consumo, as despesas com garantia podem consumir de 1% a 2% da receita total. Para uma empresa de US$ 1 bilhão, isso pode impactar os resultados em US$ 10 milhões a US$ 20 milhões. Para muitas empresas, isso pode ser o valor do orçamento de desenvolvimento de novos produtos, ou uma parte importante de suas margens de lucro.
Além do impacto monetário direto, falhas repetidas de produtos podem ter um efeito prejudicial na reputação da empresa, levando à perda de mercado.
Então, o que uma empresa pode fazer para reduzir o custo da garantia e manter sua reputação? O primeiro e mais importante passo é entender o que causa os pedidos de garantia. Depois, tomar medidas para reduzir ou eliminar essas causas.
As três principais causas de reclamações de garantia
Os pedidos de garantia surgem principalmente porque um produto falha ao executar o uso ou a função pretendida. Em geral, são três as principais causas de reclamações de garantia, chamadas de 3P’s:
Produto: Um design de produto inadequado leva a problemas de confiabilidade.
Processo: Um projeto de fabricação inadequado leva a variações de qualidade e tolerância.
Pessoas: O uso inadequado do produto leva a falhas em campo.
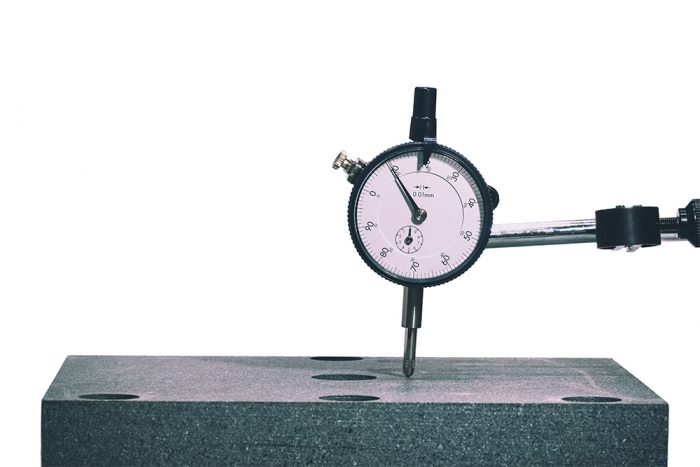
Projetos de fabricação inadequados podem levar a problemas de tolerância quando os produtos estão fora da especificação.
A maioria das pesquisas na área de garantia mostra que design de produto e processos são as principais causa de falha em campo. Também são essas as áreas onde os engenheiros podem realizar melhorias diretas. Portanto, vamos focar em como a melhoria da confiabilidade (design de produto) e da qualidade (variação do processo) pode reduzir drasticamente os custos com garantia.
Deve-se notar que os termos confiabilidade e qualidade são frequentemente usados de forma intercambiável para descrever as taxas de falha do produto. No entanto, eles têm significados muito diferentes. A qualidade mede o processo de fabricação comparando o desempenho do produto em relação a um conjunto de especificações quando sai da linha de produção. A confiabilidade, por outro lado, mede a qualidade dos produtos ao longo do tempo e em campo. De forma simples, a confiabilidade é uma função do processo de design, enquanto a qualidade é o resultado do processo de fabricação.
Design para Confiabilidade (Design for Reliability – DfR)
A confiabilidade é geralmente medida como a probabilidade de um item executar uma função, sem falha, por um determinado período de tempo.
Se uma empresa consegue obter confiabilidade em sua verdadeira forma, a garantia não é mais um problema. Isso só pode acontecer se a confiabilidade for incorporada ao design durante o estágio inicial do desenvolvimento do produto.
Tradicionalmente, a modelagem física combinada com a análise dos modos de falha e seus efeitos (FMEA, da sigla em inglês) têm sido os principais métodos para se obtter confiabilidade nos projetos de produtos. No entanto, esses métodos não estão acompanhando as demandas atuais do mercado para confiabilidade do produto.
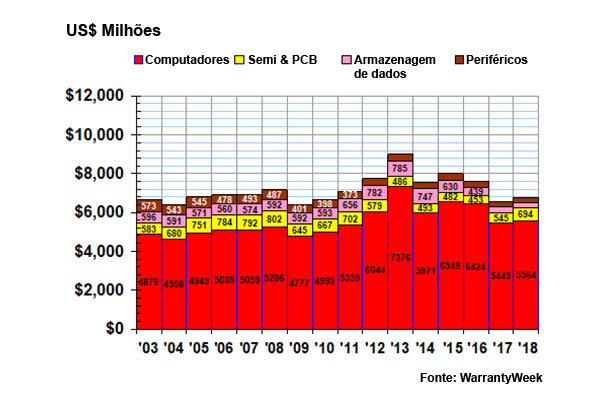
Gráfico dos pedidos de garantia da indústria de computadores pagos por empresas nos EUA (em milhões de dólares, 2003-2018). Imagem cortesia de Warranty Week, 2 de maio de 2019.
Atender aos requisitos de confiabilidade através da construção de consecutivos modelos físicos é caro e consome tempo – portanto, é ineficiente. A previsão de possíveis modos de falha usando FMEA também pode ser insuficiente, pois se baseia em métodos estatísticos puros.
Hoje, temos poderosas ferramentas que fornecem projetos robustos de maneira rápida e econômica. Por exemplo, você pode usar um software de simulação de design baseado na física da falha. Ele permite que você teste vários cenários de design em questão de horas, com um alto nível de confiança – comparado a semanas ou meses nos testes com modelos físicos.
Quando o design é baseado nos princípios de física, química e engenharia, a confiabilidade do produto tende a ser alta. Portanto, as simulações de física da falha são algumas das maneiras mais eficazes de se reduzir os custos de garantia.
Projeto de Processo para Six Sigma (DFSS)
A qualidade de um produto pode ser vista como o conjunto de recursos e características que contribuem para sua capacidade de atender às especificações – conforme definido pelo design do produto. É verdade que não existem dois produtos ou peças fabricados exatamente da mesma maneira – existe variação em todos os processos de fabricação. Ainda assim, enquanto os produtos estiverem dentro da tolerância, a peça ou produto são considerados bons.
No entanto, a variação nas especificações ainda pode levar a falhas do produto em campo. Isso aumenta o custo da garantia e a insatisfação do cliente. A Função de Perda de Taguchi descreve bem esse cenário. Ele afirma que qualquer variação do desempenho nominal começará a gerar insatisfação do cliente e custo para o produtor.

A interpretação boa / não boa do gráfico de perdas (à esquerda) mostra o conhecimento convencional de que, enquanto seu produto estiver em tolerância, o cliente geralmente ficará satisfeito. A realidade está mais próxima do gráfico que mostra a interpretação contínua da perda de Taguchi (à direita), onde não há “ponto de ruptura”. Aqui, à medida que o desempenho do produto se afasta do nominal, a insatisfação do cliente aumenta exponencialmente.
Como resultado, muitas ferramentas e técnicas foram desenvolvidas para melhorar a qualidade do produto. Um dos métodos considerados mais bem-sucedidos é o design para seis sigma (DFSS, da sigla em inglês). O DFSS combina o princípio de manufatura enxuta com seis sigma para eliminar ou reduzir a variação na fonte.
No geral, a má qualidade e a confiabilidade continuam custando às empresas milhões de dólares em custos de garantia. Isso representa uma grande oportunidade para os engenheiros melhorarem projetos inadequados e variações excessivas. Com o DfR e o DFSS, temos as ferramentas certas disponíveis para eliminar as causas principais de falha do produto e custos com garantia.