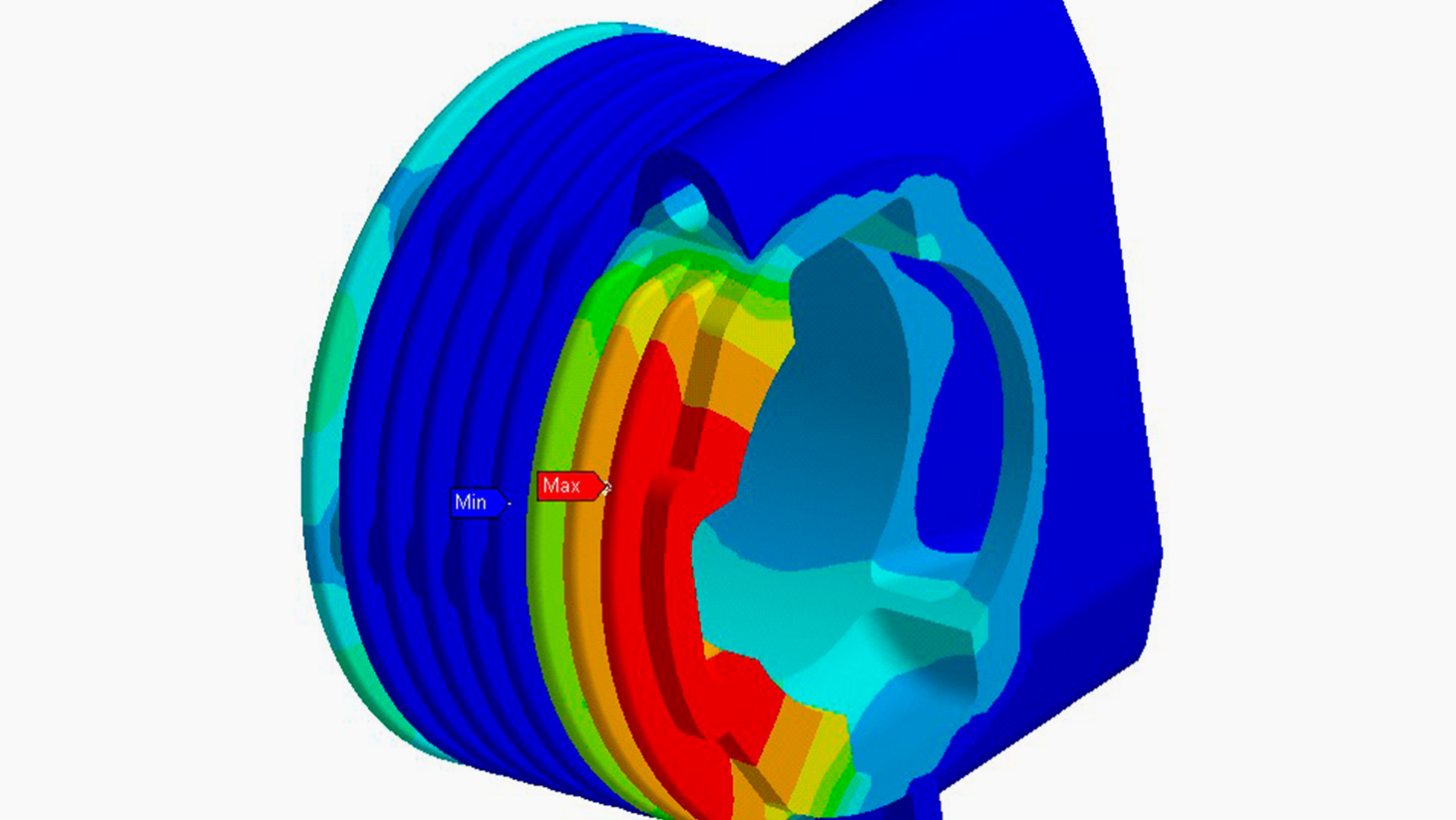
Como projetar componentes para fadiga termomecânica (TMF)
O setor automotivo passa por uma fase de transformação. As tendências do setor exigem cada vez mais inovação, para que os componentes automotivos se tornem mais leves, menores e mais eficientes.
Inúmeras indústrias já estão seguindo essa tendência, fazendo adaptações e trazendo produtos inovadores para o mercado. A indústria eletrônica, por exemplo, está aumentando a densidade de energia de seus produtos, que estão cada vez menores. Enquanto isso, o setor de transportes está exigindo turbocompressores mais eficientes em conjunto com veículos mais leves.
Acesse o webinar gratuito O futuro da indústria automotiva e o papel da simulação para conhecer os projetos de vanguarda no transporte e mobilidade.
Para os engenheiros, essas demandas podem se traduzir em relatórios sobre o aumento das cargas termomecânicas durante o processo de redução de peças. O desafio é que essas cargas influenciam a durabilidade geral do componente graças à fadiga termomecânica (TMF). Como resultado, manter as cargas constantes, quanto mais aumentá-las, enquanto projetar uma peça menor não é tarefa fácil.
O que é fadiga termomecânica?
A fadiga termomecânica é uma das principais causas de falha de componentes que são expostos a variações de temperatura e cargas mecânicas ao longo do tempo. Essas cargas influenciam a durabilidade geral e a vida útil de diversos tipos de componentes, incluindo motores.
Os testes que simulam fadiga termomecânica são capazes de replicar as condições reais de serviço desses componentes e simular os efeitos complexos de tensões térmicas e mecânicas simultâneas. Porém, é necessário um método para capturar a resposta do sistema a cargas térmicas e mecânicas com alta precisão. Só assim é possível obter a revisão precisa do local e o número de ciclos necessários para ocorrer a falha do componente.
Felizmente, a simulação pode desempenhar um papel crucial na aceleração do projeto e teste de componentes que estão em risco de TMF.

Figura 1. Simulação térmica de um coletor de escape.
Saiba como prever fadiga mecânica e térmica em moldes com análise estrutural no webinar Simulação estrutural de moldes.
Aplicação da simulação computacional em testes de fadiga termomecânica
A Ansys oferece uma solução de alta fidelidade para prever os desafios multifísicos inerentes associados ao TMF.
Vamos nos aprofundar um pouco mais na indústria de energia térmica, onde as tendências estão apontando para usinas de energia ultra-supercríticas. Essas usinas estão sendo projetadas para aumentar a eficiência e reduzir as emissões.
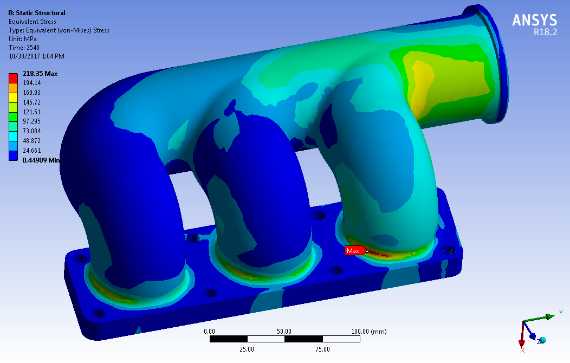
Figura 2. Simulação de estresse para um coletor de escape
O Roteiro Tecnológico da IEA: Alta Eficiência, Baixa Emissão e Geração de Energia a Carvão nos diz que essas novas usinas precisam operar em temperaturas de pico de vapor, talvez acima de 700 ° C (1290 ° F).
Além disso, essas usinas também devem operar com um fator de carga que pode variar significativamente devido à maior contribuição da energia renovável para a rede. A moral da história é que esses requisitos também estão associados a um risco maior de TMF.
Segundo a tese de John Shingledecker, metallurgical effects on long-term creep rupture in a new nickel-based alloy, as ligas convencionais não são capazes de atender aos requisitos de projeto dessas condições termomecânicas.
Em vez disso, ligas resistentes ao calor, como as baseadas em níquel, são usadas em regiões críticas para atender aos requisitos de projeto. Infelizmente, essas ligas podem tornar o projeto muito mais caro.
Desafios dos projetos de componentes
O desafio de engenharia torna-se então o projeto de componentes (como caldeiras, turbinas, válvulas e tubulações) que minimizam o uso desses materiais caros mantendo alta segurança e a função de operação do equipamento.
O engenheiro também precisa determinar como os componentes responderão às condições fora da operação normal, como em condições extremas em potencial.
As simulações Ansys permitem que você resolva uma distribuição de temperatura de alta fidelidade considerando todos os mecanismos do fluxo de calor. Por exemplo, com ferramentas de dinâmica de fluidos computacional (CFD), é possível analisar uma transferência de calor conjugada detalhada, onde todos os efeitos de fluidos e efeitos térmicos são considerados.
Os usuários também tem acesso à modelos que podem avaliar a combustão, a turbulência, a multifase, a radiação e muito mais.
Alternativamente, também é possível executar uma análise térmica no Ansys Mechanical. Nesse caso, ao invés de resolver o fluxo, o usuário assume coeficientes de transferência de calor nas interfaces de fluido. Para aumentar a precisão, no entanto, é possível determinar os coeficientes de transferência de calor de simulações de CFD.
O comportamento final da temperatura transitória é então mapeado na análise estrutural para ver como o componente se comporta em resposta às cargas térmicas e mecânicas.
O estresse e a tensão desenvolvidos para um conjunto de ciclos representativos (como mostrado nas Figuras 1 e 2) são usados para calcular onde ocorre o dano local e a vida útil do componente.
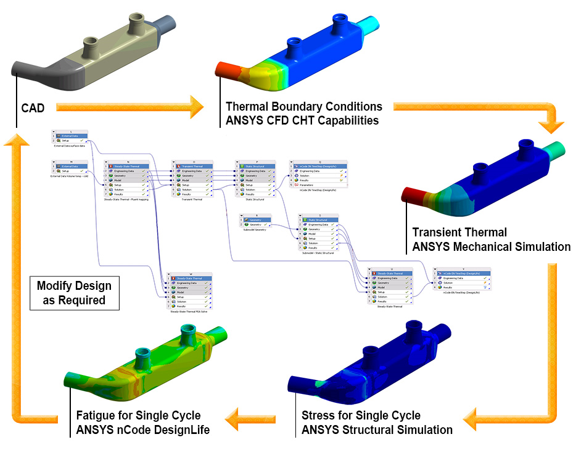
Figura 3. Fluxo de trabalho Ansys para executar uma análise do TMF.
As soluções de alta precisão e simplificação desenvolvidas pela Ansys para a fadiga termomecânica, como visto na Figura 3, são usadas em todos os segmentos da indústria para desenvolver designs inovadores usando novos materiais sob condições adversas em menos tempo.